Introduction
In the realm of quality control, AQL (Acceptable Quality Level) plays a pivotal role in ensuring products meet established standards. Understanding AQL and its significance is essential for businesses aiming to maintain high-quality outputs while minimizing costs. This introduction will explore what AQL stands for, why it matters, and provide an overview of how to read and use an AQL table effectively.
Understanding AQL and Its Importance
AQL stands for Acceptable Quality Level, a statistical measurement used to determine the maximum number of defective items considered acceptable in a sample batch. It is crucial for businesses because it helps them balance quality assurance with production efficiency, allowing them to avoid excessive costs associated with rejections or recalls. By grasping how to read an AQL table, organizations can implement more effective quality control processes that ultimately lead to customer satisfaction.
What Does AQL Stand for?
At its core, Acceptable Quality Level (AQL) represents the threshold at which a product’s quality is deemed acceptable during inspections. This concept is vital across various industries—from manufacturing to food production—where maintaining consistent quality can make or break a business's reputation. Knowing what AQL stands for sets the foundation for understanding how different inspection levels affect product quality and how companies can optimize their processes.
Overview of AQL Tables and Their Uses
AQL tables serve as practical tools that help businesses determine sample sizes and acceptance limits during inspections based on predefined standards. These tables simplify decision-making by providing clear guidelines on what constitutes acceptable quality levels across various inspection scenarios. By learning how to read an AQL table, companies can make informed choices about choosing inspection levels, sample sizes using the AQL chart, and setting appropriate acceptance limits for their inspections—all critical factors in managing defective samples effectively.
What is an AQL Table?
An AQL table is a vital tool in quality control, providing a framework for assessing the acceptability of products based on predetermined criteria. With its structured layout, it helps businesses determine acceptable quality levels (AQL) for various inspections. Understanding how to read and use an AQL table can significantly enhance your quality management processes.
Definition and Purpose of AQL
AQL stands for Acceptable Quality Level, which defines the maximum number of defective items considered acceptable in a sample batch. The purpose of an AQL table is to facilitate decision-making during inspections by providing clear guidelines on acceptable defect rates. By using this table, organizations can systematically evaluate product quality without resorting to exhaustive testing of every item.
Importance of AQL Tables in Quality Control
AQL tables are crucial in maintaining high-quality standards across industries by enabling consistent evaluation methods. They help streamline the inspection process by clearly outlining how many samples to inspect and what constitutes an acceptable level of defects. This not only saves time and resources but also aids in effective communication among stakeholders regarding product quality expectations.
Applications of AQL Tables in Different Industries
The versatility of AQL tables allows them to be used across various sectors, from manufacturing to food safety and electronics. In manufacturing, choosing inspection levels effectively ensures that products meet stringent safety standards without excessive costs or delays. Similarly, in food production, understanding how to read an AQL table helps ensure that consumer safety remains paramount while maintaining operational efficiency.
How to Read AQL Table?
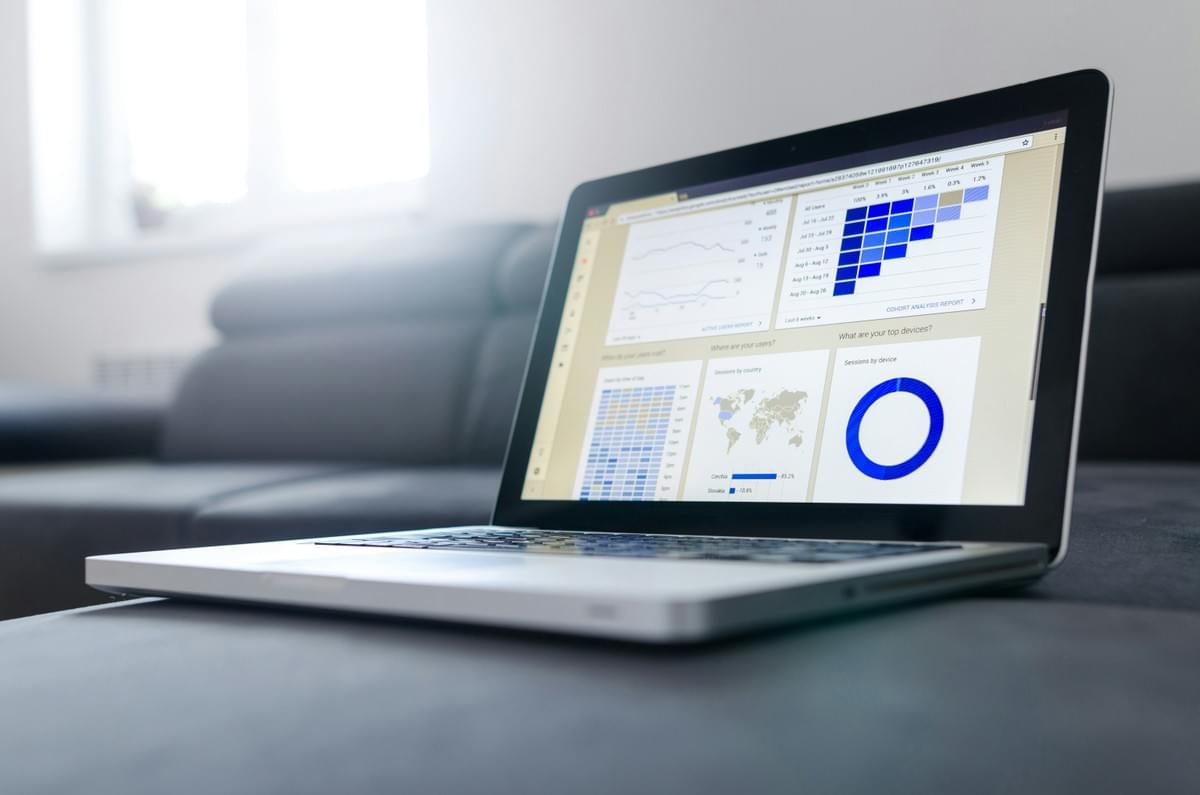
Reading an AQL table can be a bit like deciphering a secret code, but once you understand the layout and purpose, it becomes much easier. In this section, we will explore how to read an AQL table effectively, ensuring you grasp the essentials of quality control. With a solid understanding of what AQL stands for and how it applies to your inspection processes, you'll be better equipped to maintain high standards in your products.
Decoding the Columns and Rows
To begin with, let's break down the structure of an AQL table. Typically, you'll find columns that represent different sample sizes and rows that denote various acceptance quality limits (AQLs). Understanding how to read these columns and rows is crucial in choosing inspection levels and determining sample size using the AQL chart for your specific needs.
Each cell within the table provides critical information about acceptance numbers based on your chosen sample size and acceptable defect rate. For instance, if you're selecting a sample size of 200 units with an AQL of 1%, you will refer to the corresponding cell to find out how many defects are permissible before rejecting the batch. This straightforward approach helps streamline decision-making during inspections and ensures consistency in quality management.
Using AQL Standards in Practice
Now that you know how to read an AQL table, let’s discuss practical applications of these standards in real-world scenarios. When implementing these standards during inspections, it's essential to follow established protocols for choosing inspection levels based on product type and risk factors associated with defects. By understanding what does AQL stand for—essentially a measure that balances cost against risk—you can make informed decisions about product quality.
In practice, using an AQL table means aligning your inspection process with industry standards while considering factors such as customer expectations and regulatory requirements. For example, if you're manufacturing electronic components where failure rates could lead to significant safety issues, you might choose a stricter acceptance limit than if you're producing less critical items like packaging materials. This flexibility allows businesses across various sectors to adapt their quality control measures accordingly.
Common Mistakes When Reading AQL Tables
Despite their utility, there are common pitfalls when reading an AQL table that can lead to costly mistakes during inspections. One frequent error is misinterpreting sample sizes or acceptance limits; always double-check which column or row corresponds with your specific criteria before making conclusions about defect allowances or inspection levels. Additionally, some may overlook adjustments necessary for different product categories or environments when choosing acceptance limits for their inspections.
Another common mistake is assuming all defects are equal; not all flaws have the same impact on functionality or safety. Understanding what qualifies as critical versus minor defects can significantly affect decisions regarding what to do with defective samples after inspections are completed—whether they should be reworked or discarded entirely depends on this classification process! By being aware of these common errors while learning how to read and use an AQL table effectively, you'll enhance both accuracy and efficiency in quality control practices.
AQL Inspection Levels Explained
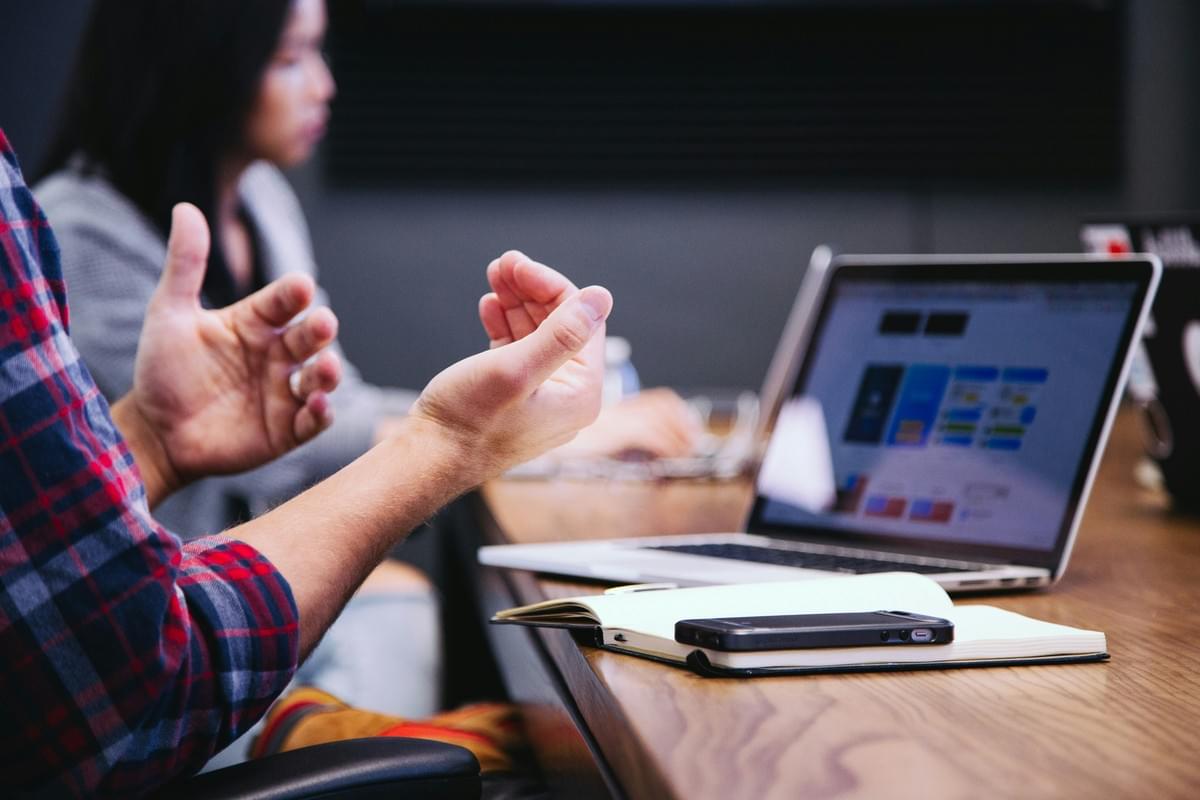
When it comes to quality control, understanding AQL inspection levels is vital for ensuring products meet specified standards. Different inspection levels dictate how thoroughly a batch will be examined, impacting both the efficiency and effectiveness of the quality assurance process. In this section, we'll uncover the various AQL inspection levels, how to choose between them, and their overall impact on quality control.
Different Levels of AQL Inspections
AQL inspection levels typically fall into three categories: general inspection level I, II, and III. Level I is the most basic and usually involves a smaller sample size; it's often used when there’s little risk associated with defects. Level II is the standard level for most situations, while Level III offers a more rigorous approach that involves larger sample sizes and stricter criteria—perfect for high-stakes industries where defects can lead to significant consequences.
Understanding these different levels is crucial when determining How to Read AQL Table effectively. Each level corresponds to specific sampling plans that help in deciding how many items should be inspected from a lot or batch based on its size. Therefore, knowing what does AQL stand for becomes essential as it provides clarity on how these tables can guide your decisions regarding inspections.
How to Choose an Inspection Level
Choosing an inspection level isn't just about picking one at random; it requires careful consideration of several factors including product type, risk tolerance, and industry standards. If you’re dealing with high-value or safety-critical items, opting for a higher inspection level might be prudent despite increased costs. Conversely, if you're inspecting low-cost items with minimal risk of defect impact, a lower level could suffice—this decision directly ties into choosing sample size using an AQL chart.
To make an informed choice regarding your Choosing Inspection Level, consider consulting historical data from previous inspections as well as feedback from stakeholders involved in production or sales processes. Additionally, understanding customer expectations can guide you toward selecting an appropriate level that meets both regulatory requirements and industry best practices.
Impact of Inspection Levels on Quality Control
The impact of your chosen inspection level on quality control cannot be overstated; it can mean the difference between catching defects early or facing costly recalls later down the line. Higher inspection levels generally yield better detection rates but may also slow down production timelines due to more extensive checks—this is where balancing efficiency with thoroughness becomes crucial in What to Do with Defective Samples.
Moreover, implementing appropriate acceptance limits during inspections ensures that you maintain product integrity while minimizing waste—a critical aspect when considering choosing acceptance limits for your inspection process. Ultimately, aligning your chosen AQL inspection levels with robust quality management systems will enhance overall product reliability and customer satisfaction.
Choosing Sample Size Using AQL Chart
When it comes to ensuring quality in manufacturing, choosing the right sample size using an AQL chart is crucial. This process is not merely about picking a number; it's about understanding what does AQL stand for? The Acceptable Quality Level (AQL) dictates how many defects are permissible in a sample size, and this can significantly influence your inspection outcomes. So, let's dive into the nitty-gritty of determining sample sizes and how they relate to the broader context of quality control.
Determining Sample Size for Inspections
Determining the appropriate sample size for inspections involves several factors that can vary based on industry standards and product types. First off, you need to consider the total lot size—this will guide you in selecting a representative sample that reflects the overall quality of your batch. Additionally, you should take into account your desired level of confidence and risk tolerance when deciding on sample sizes; this is where understanding AQL inspection levels comes into play.
For instance, if you're working with a large lot but only want to minimize risk slightly, you might choose a smaller sample size while still adhering to acceptable limits. Conversely, if you're dealing with high-stakes products where failure could lead to significant repercussions, opting for a larger sample could be wise. Remember: how to read an AQL table effectively will directly impact your decision-making process regarding these crucial aspects.
Understanding the AQL Chart
The AQL chart serves as an essential tool in any quality management toolkit; however, understanding it requires some diligence. At its core, the chart outlines different acceptance levels based on various inspection levels and lot sizes—essentially acting as your roadmap through the maze of quality assurance metrics. Knowing how to read and use an AQL table means being able to quickly identify what percentage of defects is acceptable for each specific scenario.
In practical terms, this means aligning your inspection criteria with business objectives while keeping customer satisfaction at the forefront. For example, if you’re aiming for high-quality standards in luxury goods versus everyday items, you'll need different acceptance limits reflected in your chosen sample size from the AQL chart. This nuanced comprehension allows businesses not just to comply with standards but also excel beyond them.
Factors Affecting Sample Size Decisions
Several factors come into play when choosing sample sizes using an AQL chart—each influencing how you approach inspections and ultimately impacting product quality control strategies like choosing acceptance limits for your inspection processes. One primary factor is product complexity: intricate items may require larger samples due to their potential variability in defects compared to simpler products.
Another consideration is historical data—if previous inspections have shown consistent defect rates or patterns within certain ranges, this information can guide future decisions on what constitutes an adequate sample size going forward. Lastly—and perhaps most importantly—the implications of defective samples must weigh heavily on these choices; knowing what to do with defective samples can help refine future inspections and improve overall product integrity.
Choosing Acceptance Limits for Your Inspection
Choosing acceptance limits is a crucial step in the AQL process, as it directly influences how you assess product quality. These limits help determine what constitutes an acceptable level of defects in a sample and guide you on whether to accept or reject a batch. Understanding the nuances of acceptance limits can significantly enhance your quality control processes.
Defining Acceptance Limits in AQL
Acceptance limits in AQL refer to the maximum number of defective items allowed in a sample before the entire lot is rejected. Essentially, these limits act as thresholds that dictate the quality standards your products must meet based on predetermined criteria. When determining acceptance limits, it's essential to consider factors such as customer expectations and industry standards, ensuring that they align with your overall quality objectives.
Strategies for Setting Acceptance Criteria
When it comes to setting acceptance criteria, there are several strategies you can employ to ensure they are both effective and practical. First, consider using historical data from previous inspections to inform your decisions on what constitutes an acceptable defect rate; this can provide valuable insights into realistic expectations for future batches. Additionally, involving key stakeholders—like production teams and clients—in the discussion can help create criteria that reflect both operational capabilities and customer satisfaction.
Real-World Examples of Acceptance Limits
Real-world examples illustrate how different industries utilize acceptance limits effectively within their quality control frameworks. For instance, in electronics manufacturing, a common acceptance limit might be set at 1% defective items for critical components while allowing up to 5% for non-critical parts; this reflects varying levels of risk associated with defects in different contexts. Similarly, the food industry may adopt stricter acceptance criteria due to health implications—typically allowing only a fraction of defects based on safety regulations—showing how context matters when choosing acceptance limits for your inspection.
What to Do with Defective Samples
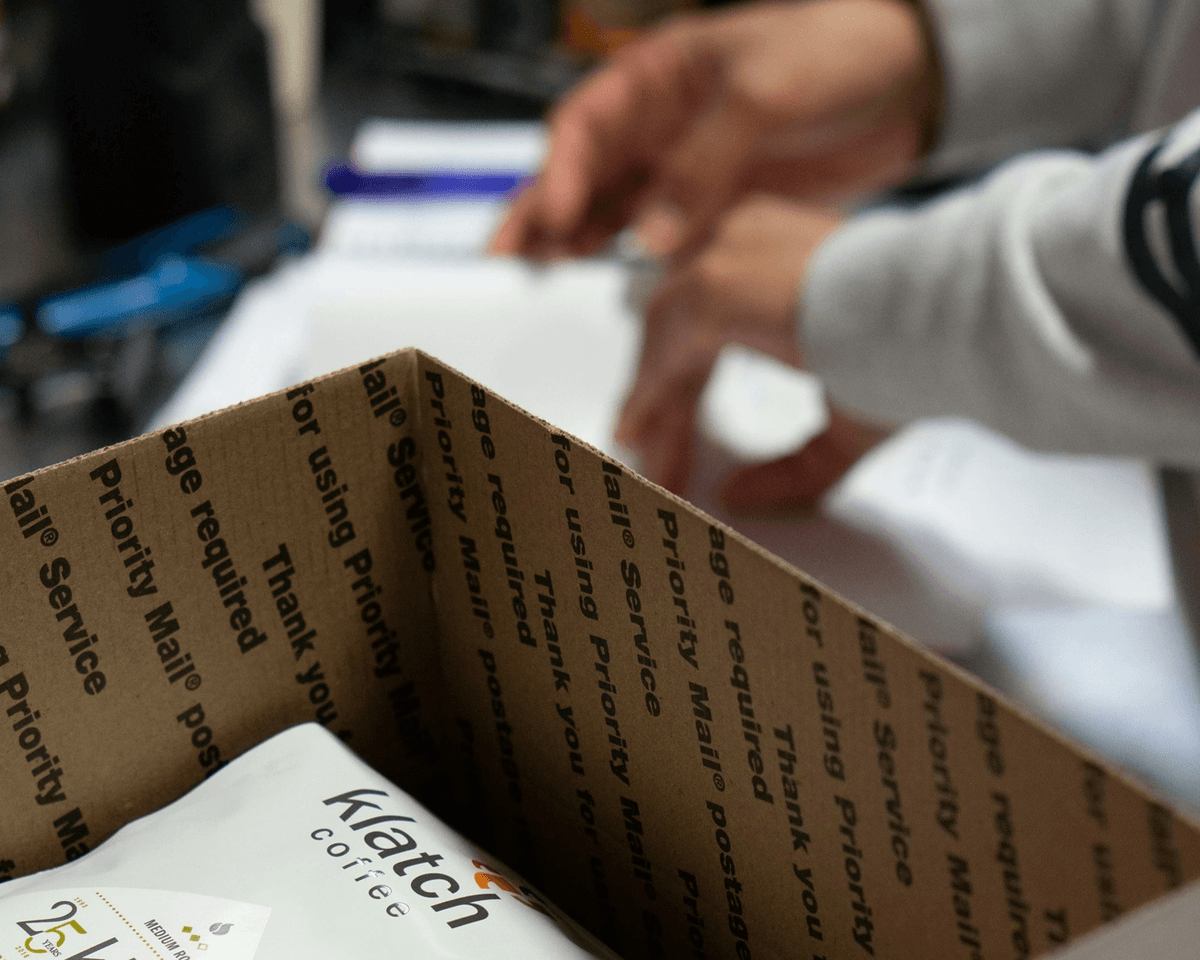
When dealing with defective samples, having a structured approach is crucial for maintaining quality control. First and foremost, you should document every defect meticulously, noting the type and severity of each issue. This documentation not only aids in understanding the scope of the problem but also assists in future inspections, especially when considering how to read AQL tables effectively.
Procedures for Handling Defective Products
Once defects are identified, it’s essential to have clear procedures in place for handling these products. Start by segregating defective items from acceptable ones to prevent any mix-up during further analysis or inspection phases. Following that, assess whether the defects can be repaired or if the products need to be discarded entirely; this decision can significantly impact your overall quality management strategy.
Additionally, communicate your findings with relevant stakeholders and consider conducting a root cause analysis to understand why these defects occurred in the first place. This proactive step not only helps you refine your processes but also informs choices regarding acceptance limits for your inspection and how to read and use an AQL table effectively in future assessments.
Importance of Defective Sample Analysis
Analyzing defective samples is not merely a formality; it's an integral part of enhancing your quality control processes. By examining these samples closely, you gain insights into recurring issues that may affect product performance or customer satisfaction. This analysis can directly influence decisions on choosing inspection levels and sample sizes using AQL charts since understanding defect patterns allows for more targeted inspections.
Moreover, thorough analysis enables companies to adjust their acceptance limits based on real data rather than assumptions, leading to more robust quality assurance practices overall. It’s akin to having a crystal ball that reveals where improvements are needed most urgently—an invaluable asset when striving for excellence.
Role of China Inspection Pro in Quality Management
In navigating the complexities of defective sample management, partnering with specialized firms like China Inspection Pro can make all the difference. These experts provide tailored solutions that encompass everything from understanding what does AQL stand for? to implementing effective procedures for handling defective products efficiently. They help streamline processes related to choosing inspection levels and setting appropriate acceptance limits based on comprehensive data analysis.
China Inspection Pro also offers valuable training resources on how to read AQL tables effectively so your team feels confident making informed decisions during inspections. Ultimately, their expertise ensures that you’re not just reacting to defects but proactively improving product quality across the board.
Conclusion
In wrapping up our exploration of AQL tables and their significance in quality control, it's clear that understanding how to read an AQL table is crucial for industries aiming to maintain high standards. From deciphering what does AQL stand for to mastering the intricacies of choosing inspection levels, every aspect plays a vital role in ensuring product quality. By familiarizing yourself with the various applications of AQL tables, you can significantly enhance your operational efficiency and minimize defects.
Key Takeaways on AQL Tables
AQL tables are indispensable tools that help organizations gauge product quality through statistical sampling methods. Understanding how to read and use an AQL table not only clarifies acceptance criteria but also aids in choosing sample sizes effectively. Remember, the key takeaway is that these tables provide a structured approach to managing quality assurance, making them essential for any business striving for excellence.
Enhancing Your Quality Control Processes
To truly enhance your quality control processes, it's important to integrate the insights gained from AQL tables into your daily operations. This means not just knowing how to read an AQL table but also applying it when choosing sample sizes using an AQL chart and determining acceptance limits for inspections. The more adept you become at utilizing these tools—like understanding inspection levels—the better equipped you'll be to handle defective samples efficiently.
Partnering with Experts like China Inspection Pro
When navigating the complexities of quality management, partnering with experts like China Inspection Pro can be a game-changer. They provide guidance on how to read an AQL table effectively while offering tailored solutions for choosing inspection levels and acceptance limits specific to your needs. With their support, you can confidently address what to do with defective samples and significantly elevate your overall quality control strategy.