Introduction
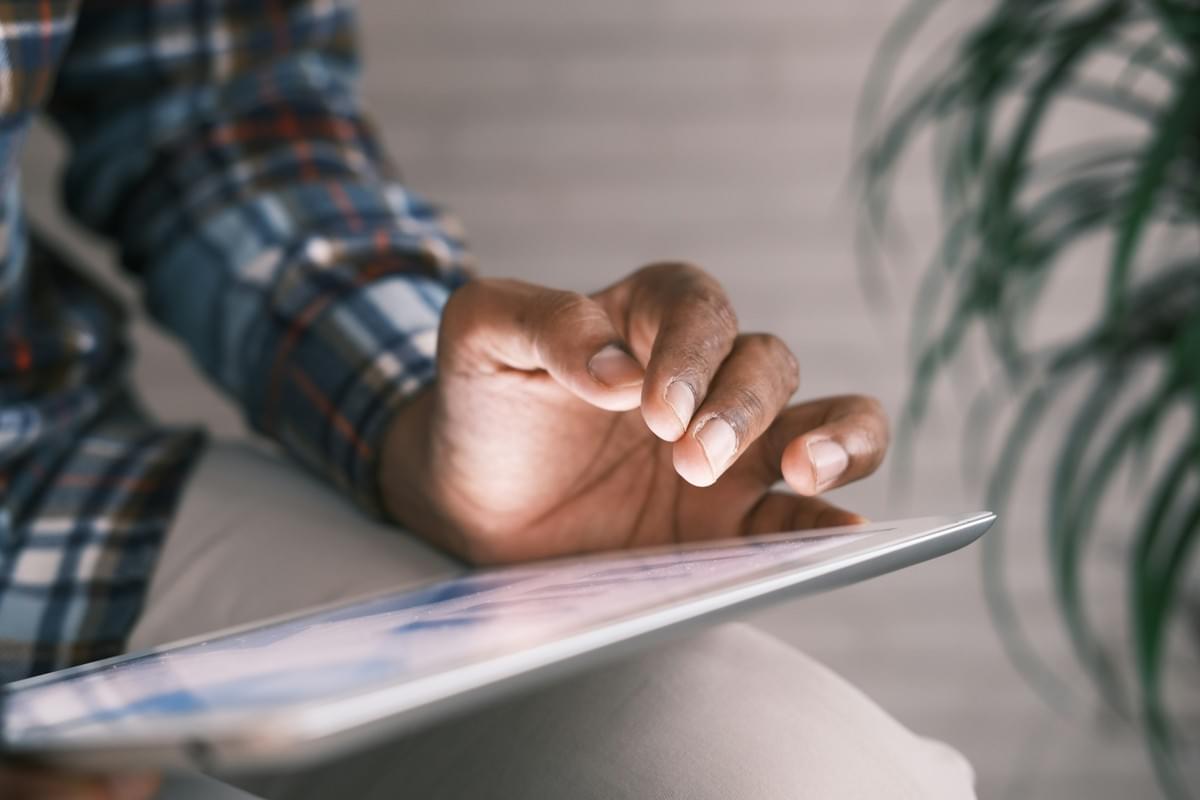
In the intricate world of supply chain management, ensuring quality and compliance is paramount. One critical tool that facilitates this process is the Supplier Corrective Action Report (SCAR). Understanding SCAR helps organizations identify non-conformance reasons determined during audits or inspections, enabling them to implement effective corrective actions.
Understanding Supplier Corrective Action Reports
What is Supplier Corrective Action Report (SCAR)? At its core, a SCAR is a formal document used to address and rectify issues related to product quality or service delivery from suppliers. By documenting the problem definition and outlining the corrective reason deployed, SCARs serve as a structured approach for continuous improvement in supplier relationships and operational efficiency.
Importance of SCAR in Supply Chain Management
The importance of SCAR in supply chain management cannot be overstated; it acts as a catalyst for enhancing quality assurance processes. By engaging in timely containment analysis and issuing supplier corrective action requests, organizations can swiftly address deficiencies before they escalate into larger problems. This proactive approach not only fosters better supplier collaboration but also significantly reduces costs associated with non-conformance.
Key Components of a SCAR Process
A successful SCAR process consists of several key components that ensure thorough investigation and resolution of issues. The SCAR timeline outlines the phases from initiation to closure, emphasizing timely responses to enhance problem resolution effectiveness. Additionally, roles and responsibilities within the process must be clearly defined to facilitate communication between stakeholders involved in problem definition and corrective actions taken.
What is Supplier Corrective Action Report (SCAR)?
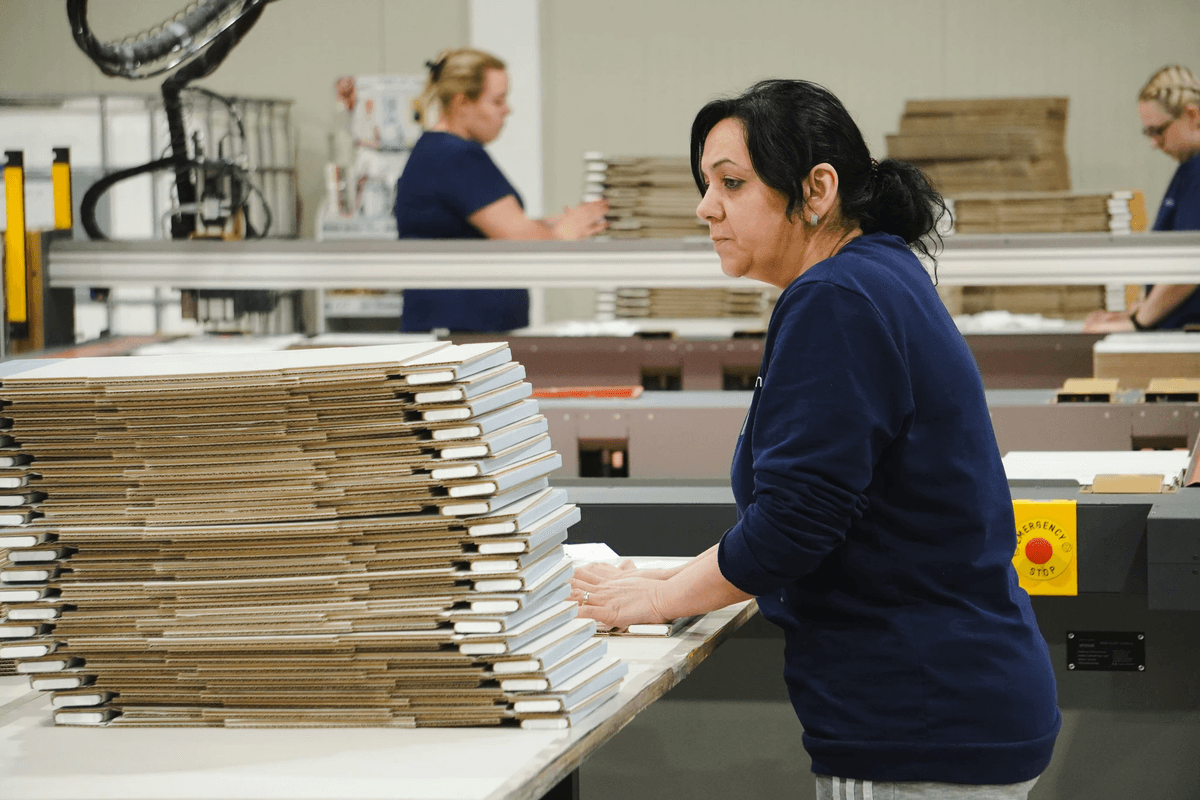
Supplier Corrective Action Reports (SCARs) are essential tools in supply chain management, designed to address and rectify issues arising from non-conformance in products or services. They serve as a formal mechanism for documenting problems, analyzing root causes, and deploying corrective actions to prevent recurrence. Understanding what a SCAR entails is crucial for organizations aiming to maintain quality assurance and enhance supplier relationships.
Definition of SCAR in Supply Chain Context
In the realm of supply chain management, a Supplier Corrective Action Report (SCAR) is defined as a structured document that outlines the necessary steps to address non-conformance issues identified with supplied goods or services. This report not only highlights the problems but also delineates the corrective actions required to resolve them effectively. By implementing a SCAR process, organizations can ensure that they systematically tackle quality issues while fostering accountability among suppliers.
Historical Background of SCAR Implementation
The implementation of SCARs can be traced back several decades when industries began recognizing the importance of quality control and supplier accountability in manufacturing processes. Initially adopted by sectors like aerospace and automotive, the SCAR framework has evolved significantly over time, adapting to various industry needs and technological advancements. Today, it serves as a vital component in many sectors where quality assurance is paramount, ensuring that companies remain competitive while upholding high standards.
Industries that Benefit from SCAR Reporting
Numerous industries benefit from implementing Supplier Corrective Action Reports (SCAR), including automotive, aerospace, pharmaceuticals, electronics, and food production. These sectors often face stringent regulatory requirements and high-quality expectations from consumers; thus, effective SCAR processes are critical for maintaining compliance and customer satisfaction. By utilizing SCARs effectively within these industries, companies can streamline their problem definition processes and enhance their containment analysis efforts.
SCAR Timeline: A Step-by-Step Process
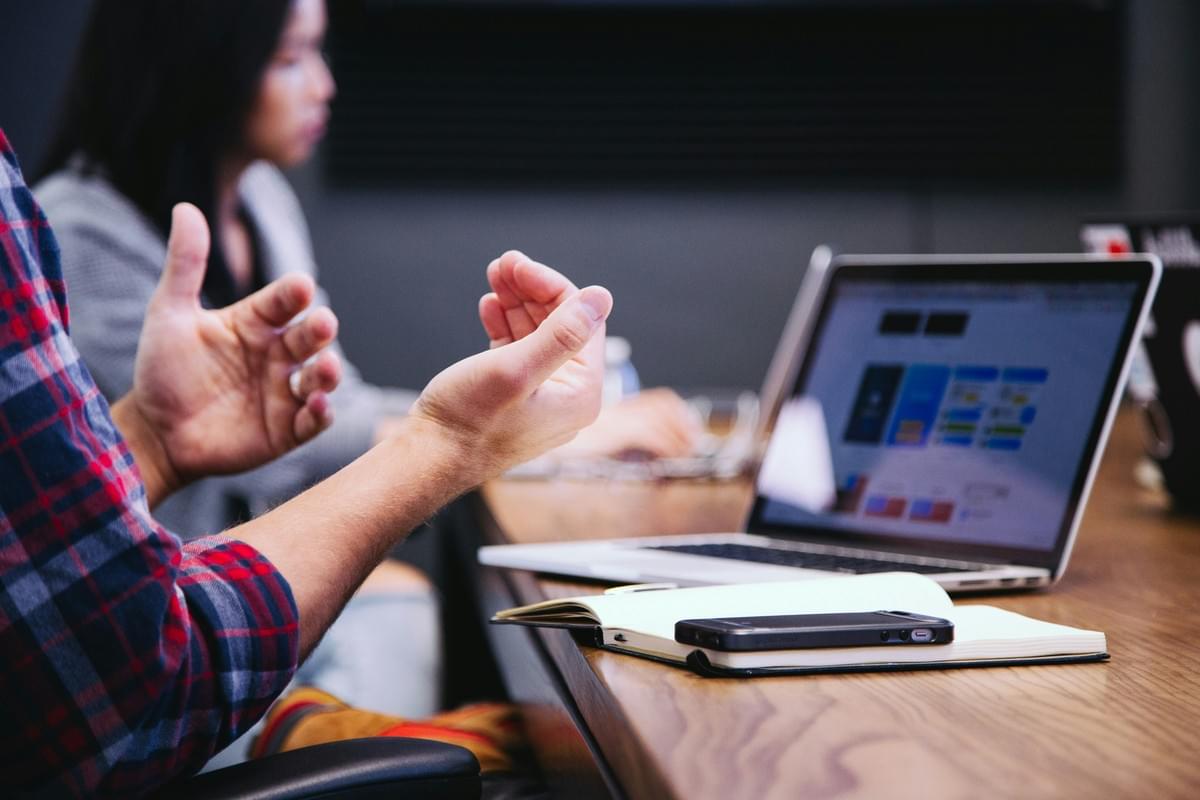
Navigating the SCAR timeline is crucial for effective problem resolution within supply chains. Understanding the phases of SCAR initiation helps organizations streamline their responses and ensures that corrective actions are not only timely but also effective. This structured approach aids in determining the non-conformance reason, which is vital for deploying corrective measures.
Phases of the SCAR Initiation
The SCAR initiation process begins with identifying a non-conformance issue, which triggers the need for a Supplier Corrective Action Request (SCAR). Once an issue is identified, stakeholders must gather relevant data to clarify what went wrong and why—this is where problem definition comes into play. Following this, containment analysis is conducted to implement immediate solutions that prevent further issues while a more permanent corrective action plan is developed.
Importance of Timely Responses in SCAR
Timeliness in responding to a SCAR cannot be overstated; it directly impacts how quickly issues are resolved and prevents potential escalation. Delays can lead to increased costs, strained supplier relationships, and even damage to brand reputation, making it imperative that all involved parties act swiftly upon receiving a Supplier Corrective Action Request. By adhering to established timelines, organizations can ensure that corrective reasons are deployed effectively and efficiently.
How Timelines Impact Problem Resolution
The timeline set during the SCAR process serves as a roadmap for all stakeholders involved in resolving the identified issues. Each phase—from initial identification through containment analysis—requires careful attention to deadlines; missing these can result in prolonged problems or repeated non-conformance reasons determined previously. Ultimately, adhering to these timelines not only accelerates problem resolution but also fosters accountability among suppliers, enhancing overall supply chain efficiency.
Problem Definition in SCAR Initiatives
Defining the problem accurately is a cornerstone of the Supplier Corrective Action Report (SCAR) process. A clear understanding of issues allows teams to address root causes effectively, thereby ensuring that corrective actions are relevant and impactful. This phase sets the stage for the subsequent SCAR timeline, where timely responses can significantly influence overall outcomes.
Identifying Issues through Root Cause Analysis
Root cause analysis is a systematic approach used to identify the underlying reasons for non-conformance issues within a supply chain. By asking why multiple times, teams can peel back layers of symptoms to uncover the true source of problems, which is essential in developing effective corrective measures. This analysis not only aids in defining problems accurately but also informs how corrective reason deployed will be structured to prevent recurrence.
The Role of Quality Control in Problem Definition
Quality control plays an indispensable role in problem definition during SCAR initiatives by providing critical data and insights into non-conformance reasons determined during inspections or audits. By leveraging quality metrics and historical data, organizations can pinpoint exactly where processes may have faltered and why issues occurred in the first place. This proactive approach ensures that any Supplier Corrective Action Request issued is based on solid evidence rather than assumptions.
Techniques for Effective Problem Identification
Effective problem identification techniques include brainstorming sessions, fishbone diagrams, and failure mode effects analysis (FMEA). These methods foster collaborative discussions among team members while enabling a thorough exploration of potential issues within processes or products. By employing these techniques consistently throughout the SCAR timeline, organizations can ensure that they are not just treating symptoms but addressing core issues that lead to non-conformance.
Containment Analysis: Immediate Solutions
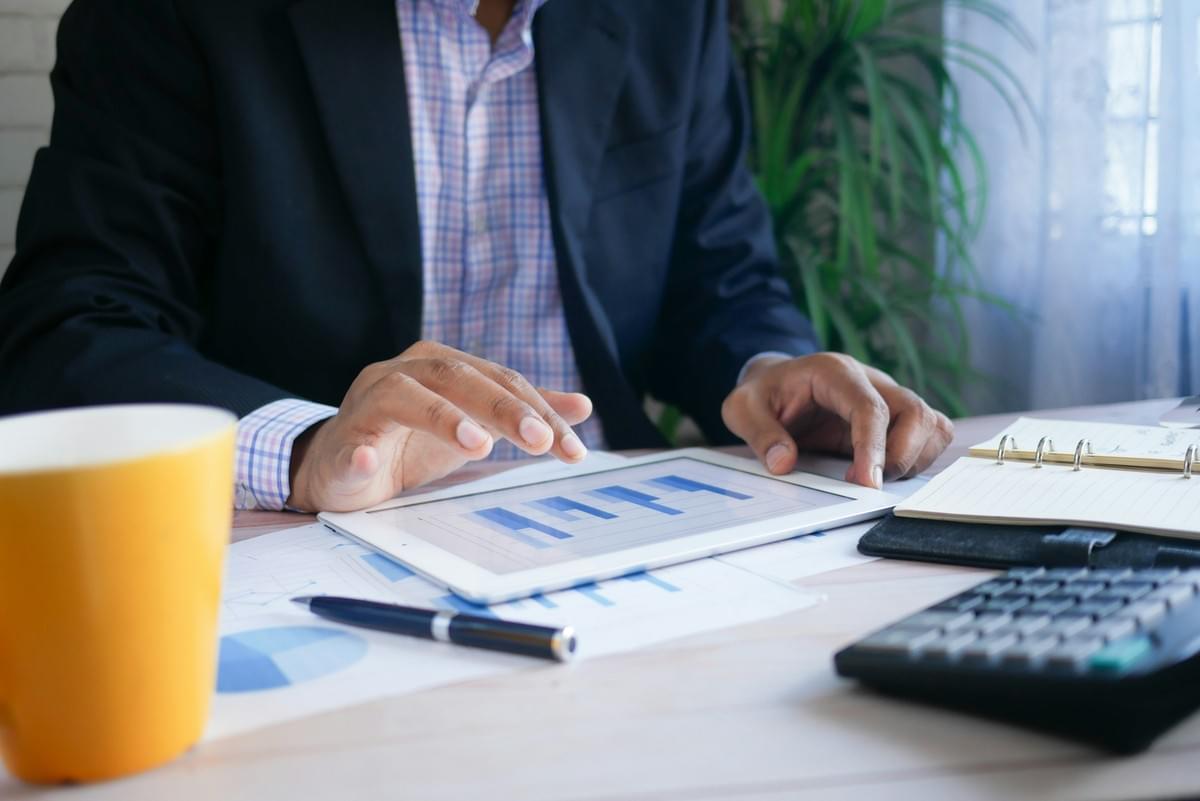
In the realm of Supplier Corrective Action Reports (SCAR), containment analysis serves as a critical first step in addressing non-conformance issues. This phase is all about implementing immediate solutions to prevent further impact on the supply chain while a more permanent corrective action is developed. By focusing on containment, organizations can effectively stabilize their operations and mitigate risks associated with quality failures.
Steps to Implement Containment Measures
Implementing effective containment measures involves several key steps that ensure swift action against identified issues. First, it's essential to gather all relevant data regarding the problem definition and non-conformance reason determined during the SCAR process. Next, cross-functional teams should be assembled to brainstorm potential containment strategies, assessing which corrective reasons deployed will provide the most immediate relief while keeping long-term goals in mind.
Once options are identified, organizations must prioritize actions based on urgency and feasibility, ensuring that everyone involved understands their roles and responsibilities in executing these measures. The SCAR timeline plays a crucial role here; timely responses can significantly affect how quickly containment actions are put into place and how effectively they mitigate risk until a permanent solution is implemented.
Monitoring and Adjusting Containment Actions
Monitoring the effectiveness of containment actions is just as important as implementing them in the first place. Regular assessments should be conducted to evaluate whether these immediate solutions are successfully addressing the problem or if adjustments are necessary. By continuously reviewing performance metrics related to quality control and supplier interactions, organizations can determine if their initial corrective reasons deployed were appropriate or if new strategies need to be considered.
Adjustments may involve re-evaluating existing measures or even escalating issues that require more robust interventions—essentially keeping an eye on whether these actions align with overall objectives for quality assurance within the supply chain. This iterative process ensures that companies remain agile in their approach while reinforcing why a SCAR is necessary: it not only addresses current problems but also helps prevent future occurrences through ongoing improvement initiatives.
Examples of Effective Containment Strategies
Effective containment strategies can vary widely depending on industry specifics but generally share some common traits that make them successful within SCAR initiatives. For instance, one common approach involves isolating affected products from circulation until further analysis can determine their status—this tactic minimizes risk while allowing time for thorough investigation into root causes behind non-conformance reasons determined during initial assessments.
Another strategy might include implementing additional inspection protocols for incoming materials from suppliers known to have had recent quality issues—this proactive measure allows companies to catch potential problems before they escalate further down the production line, thereby enhancing overall product integrity. In both cases, clear communication with suppliers about corrective actions taken fosters collaboration and reinforces relationships built upon trust—a key component of effective supply chain management.
Supplier Corrective Action Request Issued
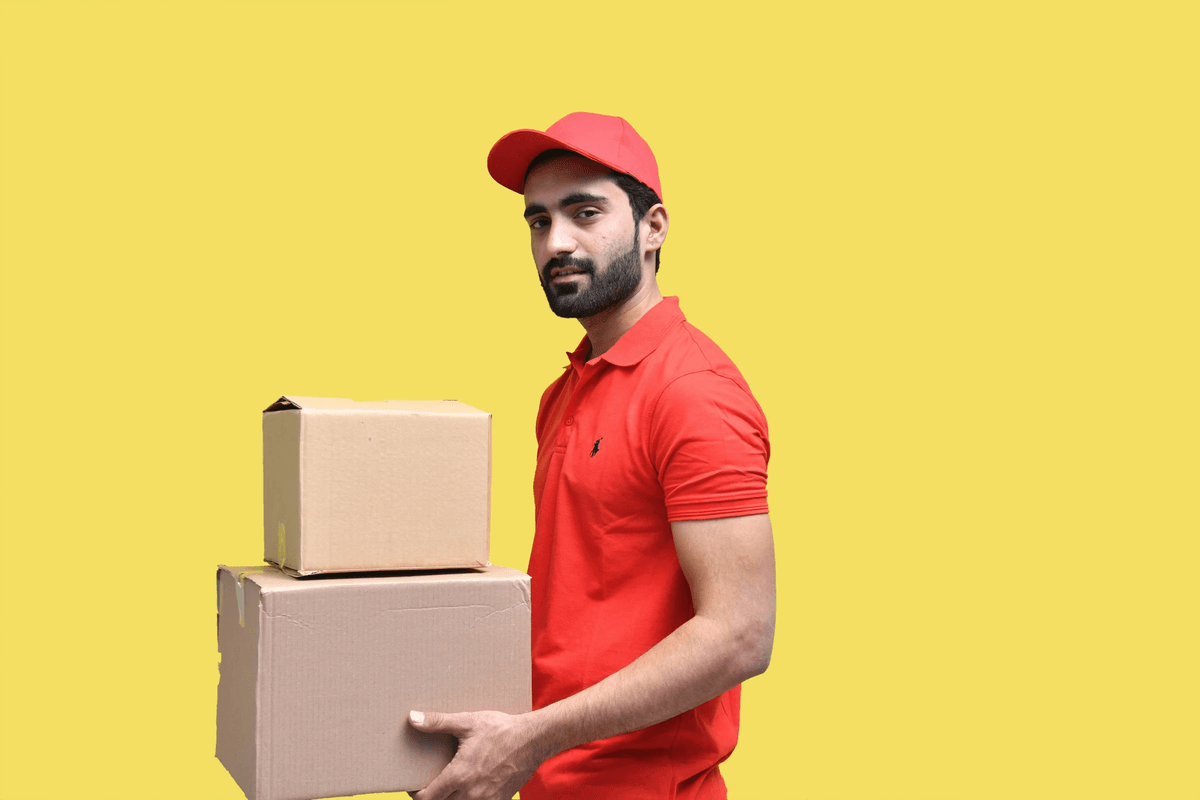
Issuing a Supplier Corrective Action Request (SCAR) is a critical step in addressing non-conformance issues within the supply chain. Understanding when and how to issue a SCAR can significantly impact the SCAR timeline and overall efficiency of problem resolution. A well-timed SCAR not only identifies the problem but also paves the way for effective containment analysis and corrective actions.
When and How to Issue a SCAR
A SCAR should be issued promptly after identifying a non-conformance reason determined during quality assessments. The timing is crucial; delays can lead to further complications, making it harder to contain the issue effectively. To initiate this process, gather all relevant data regarding the problem definition, including specifics on what went wrong and potential impacts on operations.
When drafting a SCAR, clarity is key—ensure that all details are provided succinctly, including the nature of the non-conformance reason determined and any previous corrective actions attempted. This information will help suppliers understand the urgency of your request and facilitate quicker resolutions. By establishing a clear communication channel early in this process, you set up both parties for success in deploying corrective reasons efficiently.
Roles and Responsibilities in the SCAR Process
In any SCAR process, clearly defined roles are essential for effective collaboration between stakeholders. Typically, quality assurance teams spearhead the issuance of SCARs by analyzing data from containment analysis efforts and determining root causes behind non-conformances. However, suppliers also play an integral role; they must respond promptly to requests while providing insights into their own processes that may have contributed to issues.
Each party involved should understand their responsibilities: while internal teams focus on problem definition and monitoring progress, suppliers need to develop corrective actions based on feedback received through SCARs. This collaborative approach ensures that both sides are accountable for addressing issues effectively while fostering stronger supplier relationships over time. Remember that communication throughout this process is vital; regular updates can help maintain momentum toward resolution.
Collaborating with Suppliers on Corrective Actions
Collaboration with suppliers during the SCAR process is not just beneficial—it's necessary for achieving lasting solutions to recurring problems identified through quality assessments. Engaging suppliers early helps them understand your expectations regarding containment analysis outcomes and encourages them to take ownership of corrective actions deployed in response to identified issues.
To foster productive collaboration, consider scheduling regular meetings or check-ins where both parties can share progress updates on agreed-upon actions stemming from issued SCARs. This open dialogue not only helps clarify roles but also allows for adjustments based on real-time feedback about what's working or what needs reevaluation regarding problem definition or containment strategies employed thus far.
Ultimately, why is a SCAR necessary? It bridges gaps between suppliers' capabilities and your organization's quality standards—leading to improved processes across both sides of the supply chain equation!
Why is a SCAR Necessary for Quality Assurance?
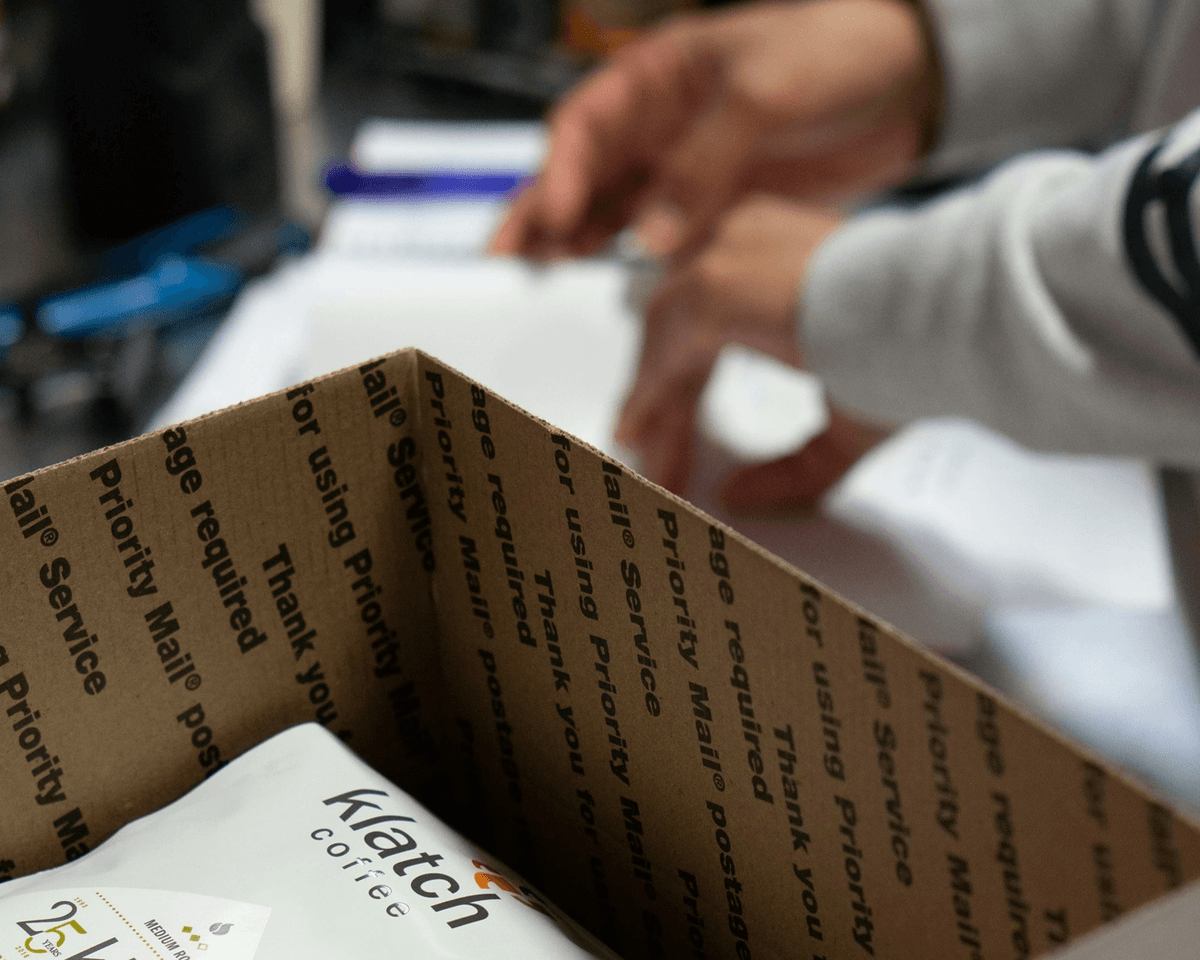
In the realm of quality assurance, understanding the necessity of a Supplier Corrective Action Report (SCAR) cannot be overstated. A SCAR not only identifies and resolves issues but also plays a pivotal role in ensuring that non-conformance reasons are thoroughly determined and addressed. By deploying corrective actions effectively, organizations can mitigate risks associated with product defects and service failures.
Understanding Non-conformance Reason Determined
Determining the non-conformance reason is essential for any SCAR process, as it lays the foundation for effective problem definition and subsequent containment analysis. When a supplier fails to meet specified requirements, identifying whether the issue stems from material defects, process errors, or human oversight is crucial. Understanding these root causes allows companies to deploy corrective reasons that address not just symptoms but underlying problems.
Benefits of SCAR for Stakeholders
The benefits of implementing a SCAR system extend beyond immediate problem resolution; they encompass stakeholders at every level of the supply chain. For manufacturers, SCARs streamline communication and foster collaboration with suppliers when issues arise, leading to quicker resolutions and reduced downtime. Furthermore, stakeholders gain confidence in product quality as systematic corrective actions are deployed—ultimately enhancing brand reputation and customer satisfaction.
How SCARs Enhance Supplier Relationships
SCARs serve as a bridge between companies and their suppliers by promoting transparency and accountability throughout the corrective action process. When a Supplier Corrective Action Request is issued promptly following an identified issue, it sets clear expectations for resolution timelines while fostering an environment of teamwork rather than blame-shifting. This collaborative approach not only resolves current problems but also strengthens relationships by building trust—making it easier to navigate future challenges together.
Conclusion
In conclusion, the Supplier Corrective Action Report (SCAR) process is a vital tool for enhancing supply chain efficiency. By establishing a clear SCAR timeline, organizations can effectively address non-conformance issues and ensure that corrective actions are deployed promptly. The structured approach of SCAR not only resolves immediate problems but also fosters a culture of continuous improvement within the supply chain.
Enhancing Supply Chain Efficiency with SCAR
Understanding What is Supplier Corrective Action Report (SCAR)? is crucial for any organization aiming to improve its supply chain operations. A well-defined SCAR timeline allows companies to identify problems early, leading to timely responses and effective containment analysis. When issues are addressed swiftly, it reduces disruptions, enhances productivity, and ultimately contributes to better customer satisfaction.
Long-term Benefits of Implementing SCAR
Implementing a robust SCAR process provides long-term benefits that extend beyond immediate problem resolution. By consistently analyzing non-conformance reasons determined through the SCAR process, organizations can identify patterns and prevent future occurrences. This proactive stance not only improves quality assurance but also strengthens supplier relationships as both parties collaborate on corrective actions.
China Inspection Pro's Role in SCAR Facilitation
China Inspection Pro plays a pivotal role in facilitating the SCAR process by providing expertise in problem definition and containment analysis. Their support ensures that when a Supplier Corrective Action Request is issued, it is handled efficiently and effectively across all levels of the supply chain. With their guidance, organizations can navigate the complexities of SCAR implementation while ensuring compliance with industry standards.