Introduction

In the dynamic world of manufacturing, quality control serves as the backbone that ensures products meet specific standards and customer expectations. Understanding quality control essentials is vital for any business aiming to thrive in a competitive market. Quality inspections play a crucial role in this process, acting as a safeguard against defects and ensuring that products are not only functional but also reliable.
Understanding Quality Control Essentials
At its core, quality control encompasses various processes designed to ensure that products are produced consistently and meet predetermined standards. Different types of QC inspections, such as Pre-Production Inspections (PPI), During Production Inspection (DPI), and Pre-Shipment Inspection (PSI), each serve unique purposes throughout the manufacturing cycle. By familiarizing oneself with these inspection types, businesses can better navigate their quality assurance strategies and improve overall product reliability.
Importance of Inspection in Manufacturing
Inspection is not just a checkbox on a production timeline; it’s an integral part of the manufacturing process that can significantly impact product success. Implementing rigorous quality inspection benefits manufacturers by reducing waste, minimizing returns, and enhancing customer satisfaction. With effective inspections in place—be it through sample checking or piece by piece inspection—companies can identify issues early on, ensuring that only top-notch products reach consumers.
Navigating Types of Quality Control Inspections
Understanding what are the different types of inspection in quality control is essential for any manufacturer looking to optimize their processes. From comprehensive pre-production evaluations to meticulous piece by piece inspections, each type offers distinct advantages tailored to specific stages of production. By exploring these various methods—including DPI and PSI—businesses can develop robust quality control frameworks that promote efficiency and excellence throughout their operations.
Overview of Quality Control Inspections
Quality control inspections are the backbone of manufacturing, ensuring that products meet the required standards before they reach consumers. These inspections can take many forms, each tailored to different stages of production and specific quality assurance needs. Understanding what these different types of inspection in quality control entail is crucial for businesses aiming to maintain high-quality standards.
Defining Quality Control Inspections
Quality control inspections refer to systematic evaluations conducted at various stages of the manufacturing process to assess whether products meet predetermined specifications. These inspections can be categorized into several types, such as Pre-Production Inspections (PPI), During Production Inspection (DPI), Pre-Shipment Inspection (PSI), and Piece by Piece Inspection (or Sorting Inspection). Each type serves a distinct purpose, making it essential for manufacturers to implement them effectively to reap quality inspection benefits.
The Role of Inspections in Manufacturing
Inspections play a pivotal role in manufacturing by identifying defects early and ensuring compliance with both internal and external standards. By employing different types of QC inspections, manufacturers can minimize waste, reduce costs, and enhance customer satisfaction through consistent product quality. Moreover, effective monitoring throughout production helps companies adapt quickly to issues that may arise, thus safeguarding their reputation in the market.
Key Players in the Inspection Process
The inspection process involves multiple stakeholders who contribute to ensuring product quality from start to finish. Key players include manufacturers, quality control inspectors, third-party inspection agencies, and supply chain managers who all collaborate closely during various types of inspections like DPI or PSI. Each participant brings unique expertise that enhances the effectiveness of inspections and ultimately leads to improved product outcomes.
Pre-Production Inspections (PPI)
Pre-Production Inspections (PPI) are a critical step in the quality control process, ensuring that products meet specified standards before manufacturing begins. This proactive approach can save manufacturers time and money by identifying potential issues early on. By understanding what to expect during PPI, businesses can streamline their production processes and enhance product quality.
What to Expect During PPI
During a Pre-Production Inspection, expect a thorough examination of materials, components, and production processes before actual manufacturing kicks off. Inspectors will evaluate samples against specific criteria such as material integrity, compliance with specifications, and overall readiness for production. This stage often includes checking supplier documentation to ensure everything aligns with quality standards.
Benefits of Conducting Pre-Production Inspections
Conducting Pre-Production Inspections brings numerous quality inspection benefits that extend throughout the manufacturing cycle. By identifying defects or discrepancies early on, companies can avoid costly reworks or delays later in the process. Furthermore, PPI fosters better communication between manufacturers and suppliers, ultimately leading to improved relationships and enhanced product quality.
How China Inspection Pro Facilitates PPI
China Inspection Pro plays a pivotal role in facilitating effective Pre-Production Inspections by providing expert inspectors who understand local regulations and industry standards. They offer tailored solutions that cater to different types of QC inspections based on specific client needs and product categories. With their comprehensive approach to PPI, businesses can confidently navigate the complexities of global trade while ensuring adherence to quality benchmarks.
During Production Inspection (DPI)
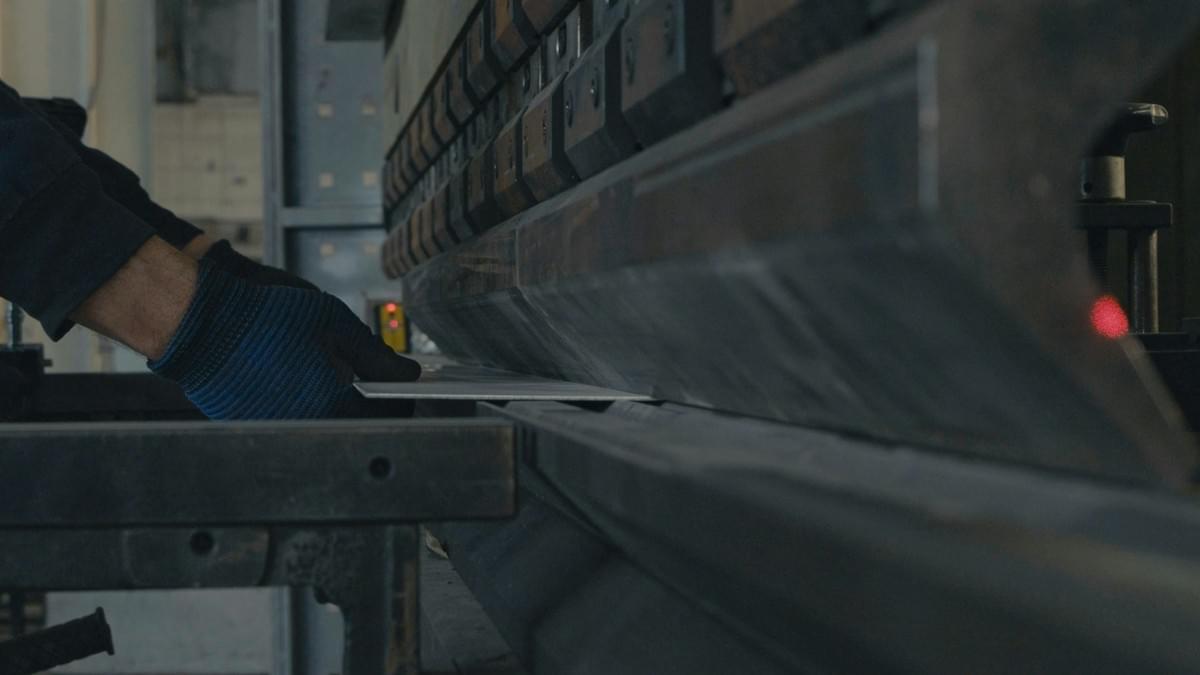
Quality control is not a one-time event; it’s an ongoing process that ensures products meet the necessary standards throughout their manufacturing journey. During Production Inspection (DPI) plays a crucial role in this continuum, allowing manufacturers to monitor quality in real-time. By integrating DPI into the production cycle, businesses can significantly mitigate risks and enhance overall product integrity.
Monitoring Quality Throughout Production
Monitoring quality throughout production involves regular checks at various stages to ensure that products are being made according to specifications. This proactive approach helps in identifying deviations from quality standards early on, which is essential for maintaining consistency across batches. DPI ensures that manufacturers are not just waiting until the end of the line, but actively engaging with the process to uphold quality inspection benefits.
Identifying Issues Early with DPI
One of the primary advantages of During Production Inspections (DPI) is its ability to identify issues early on before they escalate into larger problems. When issues are caught during production, it allows for immediate corrective actions, minimizing waste and reducing costs associated with rework or returns later down the line. This preemptive strategy aligns perfectly with other types of QC inspections like Pre-Production Inspections (PPI) and Pre-Shipment Inspections (PSI), creating a comprehensive safety net for quality assurance.
Case Studies Highlighting Effective DPI
Numerous case studies illustrate how effective DPI can transform manufacturing outcomes. For instance, a well-known electronics manufacturer implemented rigorous DPI protocols and reported a significant reduction in defect rates by 30% within six months. These success stories underscore that when businesses prioritize monitoring during production alongside Piece by Piece Inspection or Sorting Inspection techniques, they reap substantial rewards in terms of efficiency and customer satisfaction.
Pre-Shipment Inspection (PSI)
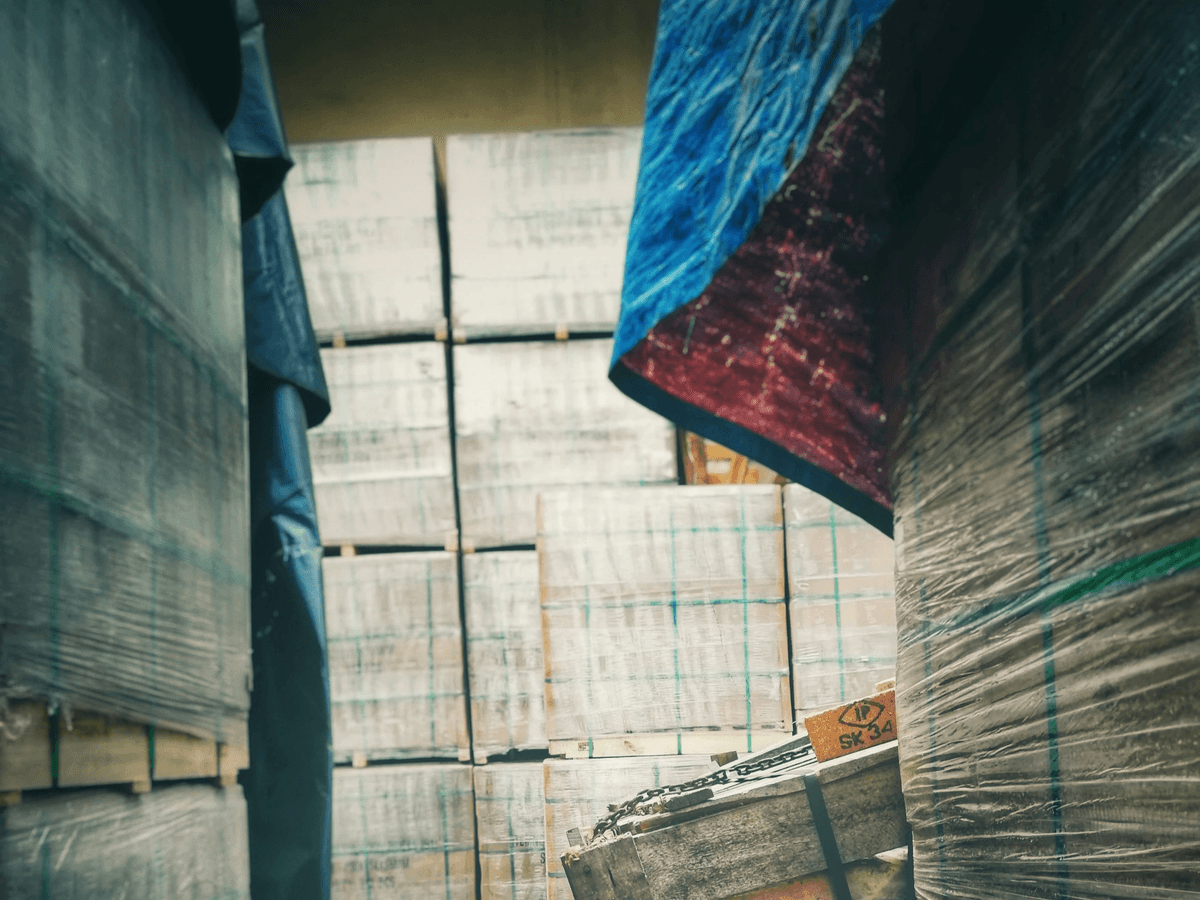
Pre-Shipment Inspection (PSI) plays a pivotal role in ensuring that products meet quality standards before they embark on their journey to customers. This stage of quality control acts as a final checkpoint, allowing manufacturers and suppliers to verify that goods are up to par with specifications and contractual obligations. By implementing PSI, businesses can avoid the costly consequences of shipping defective products, which can lead to returns, customer dissatisfaction, and damage to reputation.
Ensuring Quality Before Shipment
The primary goal of Pre-Shipment Inspection is to confirm that the products are in compliance with quality standards prior to leaving the factory. This inspection not only checks for defects but also assesses packaging and labeling requirements, ensuring everything is ready for international transport. With effective PSI procedures in place, companies can rest easy knowing they have taken proactive steps toward delivering high-quality products.
Typical Procedures in PSI
Typical procedures during Pre-Shipment Inspection involve a thorough examination of the finished goods against predefined criteria such as functionality, appearance, and safety regulations. Inspectors often carry out random sampling—this is where understanding different types of QC inspections comes into play—by selecting a certain number of items from a batch for detailed evaluation. Following this initial check, inspectors may also conduct additional tests or measurements as needed to ensure compliance with industry standards.
Why PSI is Crucial for Global Trade
In today’s interconnected world, the significance of Pre-Shipment Inspections cannot be overstated; they serve as a critical barrier against subpar products entering global markets. By ensuring that only quality goods are shipped out, businesses can enhance customer satisfaction while minimizing risks associated with product recalls or legal issues arising from non-compliance. As companies increasingly rely on international supply chains, understanding what are the different types of inspection in quality control becomes essential for maintaining competitive advantage.
Piece by Piece Inspection (Sorting Inspection)

When it comes to ensuring quality in manufacturing, the piece by piece inspection, also known as sorting inspection, plays a pivotal role. This meticulous approach allows quality control professionals to evaluate each item individually, ensuring that every product meets specified standards before it reaches the consumer. By focusing on every single piece, manufacturers can significantly reduce the risk of defects slipping through the cracks and maintain their reputation for excellence.
The Importance of Detailed Inspection
Detailed inspections are crucial in identifying subtle defects that might be overlooked during broader assessments like Pre-Production Inspections (PPI) or During Production Inspections (DPI). By examining each item closely, businesses can catch issues early and prevent costly recalls or customer dissatisfaction later on. In addition to enhancing product quality, detailed inspections provide valuable insights into production processes and can help identify areas for improvement—essentially turning potential problems into opportunities for growth.
When to Use Piece by Piece Inspections
Piece by piece inspections are particularly beneficial in scenarios where quality is non-negotiable or when dealing with high-value items that could lead to significant financial losses if defects occur. For example, industries such as aerospace or medical devices often implement sorting inspections due to the critical nature of their products. Additionally, when a previous round of inspections—like Pre-Shipment Inspection (PSI) or sample checking—has raised concerns about quality consistency, conducting a thorough piece by piece inspection can restore confidence in the final output.
Success Stories from Quality Inspection Experts
Quality inspection experts have seen firsthand how effective piece by piece inspections can transform manufacturing processes and enhance product reliability. One notable success story involves a leading electronics manufacturer that faced recurring issues with defective components reaching customers despite implementing various different types of QC inspections like DPI and PSI. By integrating sorting inspections into their workflow, they drastically reduced defect rates and improved customer satisfaction scores—demonstrating how detailed attention pays off in tangible ways.
Sample Checking
Sample checking is a crucial component of quality control that allows manufacturers to assess the quality of products without inspecting every single item. This method involves selecting a representative portion of the total production batch to evaluate against predetermined standards. By focusing on sample checking, companies can efficiently identify defects and ensure that their products meet quality expectations before they reach the market.
Understanding Sample Checking in Quality Control
When we discuss what are the different types of inspection in quality control, sample checking stands out for its efficiency and effectiveness. It serves as a practical approach to gauge product quality while minimizing time and resource expenditure. This method is especially valuable when combined with other inspections such as Pre-Production Inspections (PPI), During Production Inspection (DPI), and Pre-Shipment Inspection (PSI), providing a comprehensive overview of product integrity throughout the manufacturing process.
Advantages of Sample Inspections
The benefits of sample inspections are manifold, making them an attractive option for many businesses looking to enhance their quality control strategies. First and foremost, they save time by allowing inspectors to focus on a manageable number of items rather than evaluating every piece individually, which can be particularly tedious during Piece by Piece Inspection (or Sorting Inspection). Additionally, sample inspections help identify trends or recurring issues early on, which can lead to significant improvements in overall production quality—ultimately translating into higher customer satisfaction.
How to Implement Sample Checking Effectively
To implement sample checking effectively, it’s essential to establish clear guidelines regarding how many items will be sampled and what criteria will be used for evaluation. A well-defined sampling plan should take into account factors such as batch size, product complexity, and historical defect rates—ensuring that your sampling reflects potential issues accurately. Moreover, integrating sample inspections with other types of QC inspections like DPI or PSI can create a robust framework that maximizes the benefits of each inspection type while minimizing risks associated with poor-quality products.
Conclusion
Quality control inspections are the backbone of any successful manufacturing process, ensuring that products meet established standards before they reach consumers. Understanding the different types of inspection in quality control—such as Pre-Production Inspections (PPI), During Production Inspection (DPI), Pre-Shipment Inspection (PSI), and Piece by Piece Inspection—allows businesses to implement effective strategies for maintaining quality throughout the production cycle. By leveraging these inspections, companies can significantly enhance their product reliability and customer satisfaction.
Summary of Inspection Types
To recap, there are several different types of QC inspections that play crucial roles in the manufacturing process. Pre-Production Inspections (PPI) set the stage for quality by evaluating materials and processes before production begins, while During Production Inspection (DPI) helps monitor ongoing processes to catch issues early on. Finally, Pre-Shipment Inspection (PSI) ensures that finished products meet specifications prior to shipment, and Piece by Piece Inspection focuses on detailed assessments of individual items to guarantee quality standards are met.
Why Quality Inspections Matter for Businesses
Quality inspections provide numerous benefits that directly impact a business's bottom line. By identifying defects early through methods like Sample Checking or DPI, companies can save time and money while reducing waste associated with rework or returns. Moreover, thorough inspections foster trust with customers, enhancing brand reputation and encouraging repeat business; after all, who doesn’t appreciate receiving a product that meets their expectations?
Final Thoughts on Quality Control Strategies
Incorporating various types of inspection into your quality control strategy is not just beneficial—it's essential for success in today’s competitive marketplace. Embracing practices like Piece by Piece Inspection or PSI can help you stay ahead of potential pitfalls while ensuring your products consistently meet high standards. Ultimately, investing in robust quality inspection processes will pay dividends in customer loyalty and operational efficiency.