Introduction
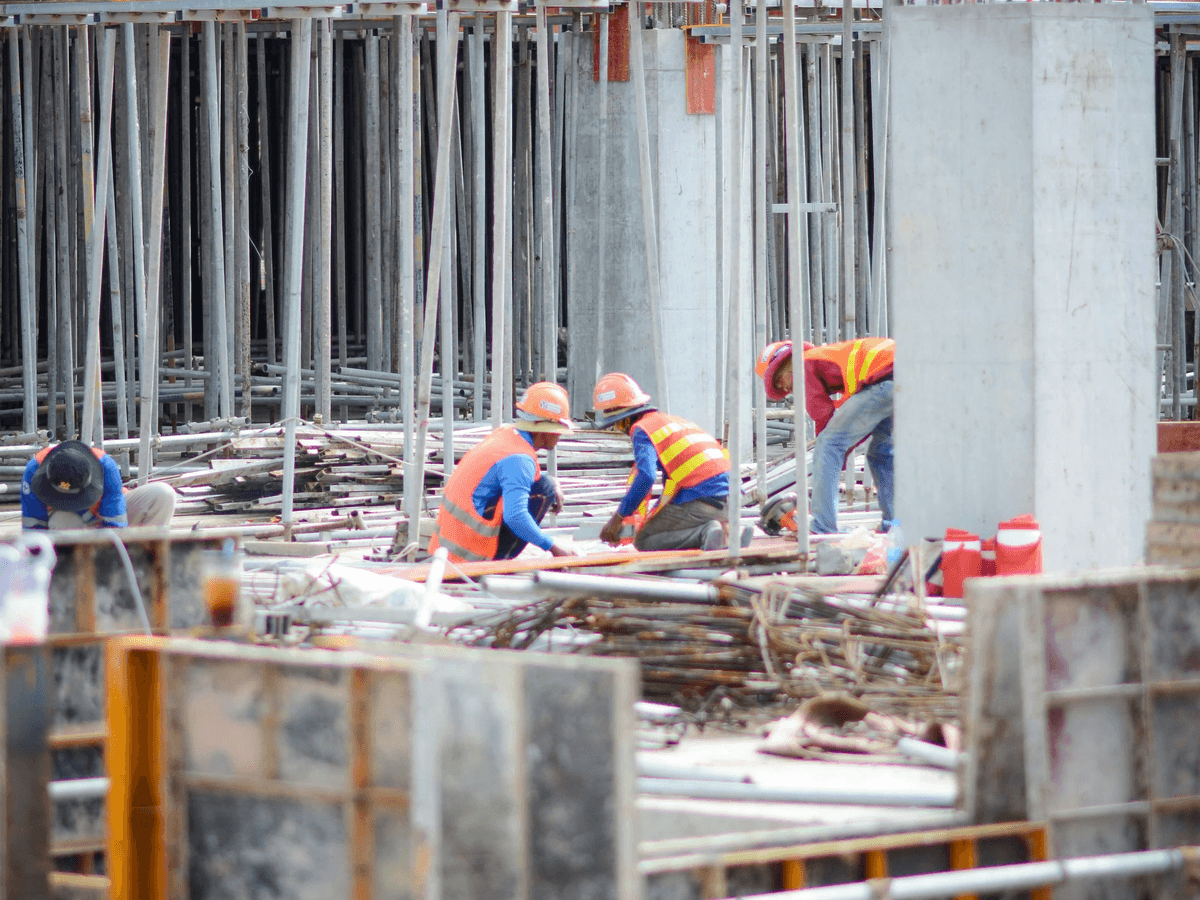
In the construction industry, the importance of quality control cannot be overstated. It serves as a foundation for ensuring that projects meet safety standards, client expectations, and regulatory requirements. Without effective quality control measures in place, construction projects can face numerous challenges that could potentially derail timelines and budgets.
The Critical Role of Quality Control
Quality control in construction is critical because it directly impacts the durability and safety of structures. Why is quality control in construction important? Well, it helps to identify defects early on, preventing minor issues from escalating into major problems down the line. By implementing rigorous quality control procedures, stakeholders can mitigate risks associated with building or structural quality issues that could endanger lives and lead to costly repairs.
Defining Quality Control in Construction
So, what is quality control in construction? At its core, it involves systematic processes aimed at maintaining high standards throughout all phases of a project—from planning and design to execution and final inspection. This ensures compliance with building codes while addressing common construction quality control procedures such as inspections and material verification processes.
The Costs of Neglecting Quality
Neglecting quality control can result in severe financial repercussions for contractors and clients alike. What are the common quality control issues in construction? These include poor workmanship in the construction industry, subpar materials leading to structural failures, and compliance violations that may incur fines or legal actions. Ultimately, overlooking these aspects not only jeopardizes project integrity but also diminishes client satisfaction—a cost that extends far beyond monetary figures.
Understanding Quality Control in Construction
Quality control in construction is a systematic process that ensures the quality of materials, workmanship, and overall project execution. It encompasses a variety of procedures and protocols designed to prevent defects and ensure compliance with specified standards. So, why is quality control in construction important? Because it not only enhances the safety and durability of structures but also protects investments by minimizing costly rework.
What Is Quality Control in Construction?
Quality control in construction refers to the measures taken to ensure that building projects meet established standards and specifications throughout their lifecycle. This includes everything from material selection to workmanship assessments, ensuring that each phase adheres to predetermined criteria. By implementing effective quality control procedures, construction firms can identify potential issues early on, addressing them before they escalate into significant problems.
The Importance of Protocols
Protocols play a crucial role in maintaining quality control within the construction industry. They provide a structured approach for inspections, testing, and documentation that helps teams stay organized and focused on quality outcomes. Without these protocols, projects risk falling prey to common issues like building or structural quality issues or poor workmanship in the construction industry—leading to delays and increased costs.
How Quality Control Mitigates Risks
Quality control mitigates risks by proactively identifying potential failures before they manifest into costly problems. Through regular inspections and adherence to established protocols, teams can address quality issues with construction materials or workmanship deficiencies early on. This not only safeguards project integrity but also enhances overall client satisfaction by delivering high-quality results consistently.
Common Construction Quality Control Procedures
When it comes to construction, having a solid grasp of common quality control procedures is paramount. These procedures are the backbone of ensuring that projects meet standards and expectations. So, what are common construction quality control procedures? Let’s dive into the nitty-gritty of inspections and testing, material verification processes, and compliance with building codes.
Inspections and Testing
Inspections and testing form the first line of defense in quality control in construction. They allow project managers to catch potential issues before they snowball into costly disasters. Why is quality control in construction important? Regular inspections help identify building or structural quality issues early on, which can save time and money down the road.
During these inspections, various aspects of the project are evaluated against predefined criteria. This ensures that every component meets safety standards and design specifications. By implementing rigorous testing protocols, teams can also address quality issues with construction materials before they become integral to the structure.
Material Verification Processes
Material verification processes play a crucial role in maintaining high-quality standards on any construction site. What is quality control in construction if not ensuring that only the best materials are used? The importance of verifying materials cannot be overstated; subpar materials can lead to significant problems like poor workmanship in the construction industry or even structural failures.
This process typically involves checking certifications, conducting laboratory tests, and reviewing supplier documentation to ensure compliance with industry standards. By adhering to strict material verification processes, contractors mitigate risks associated with inferior products that may compromise overall project integrity. Ultimately, this diligence contributes directly to reducing common quality control issues in construction.
Compliance with Building Codes
Compliance with building codes is not just a bureaucratic hurdle; it's an essential part of effective quality control in construction. These codes exist for a reason: they safeguard public health and safety while establishing minimum acceptable levels for design and construction practices. Why is quality control important in construction? Adhering to these codes helps prevent building or structural quality issues that could endanger lives or lead to costly legal repercussions.
Regular audits ensure that every phase of a project aligns with local regulations before moving forward—this includes everything from electrical systems to fire safety measures. Non-compliance can result not only in fines but also delays that can derail timelines and budgets significantly. Therefore, maintaining compliance is a proactive way to enhance overall project success while minimizing risk factors associated with poor workmanship.
Identifying Common Quality Control Issues
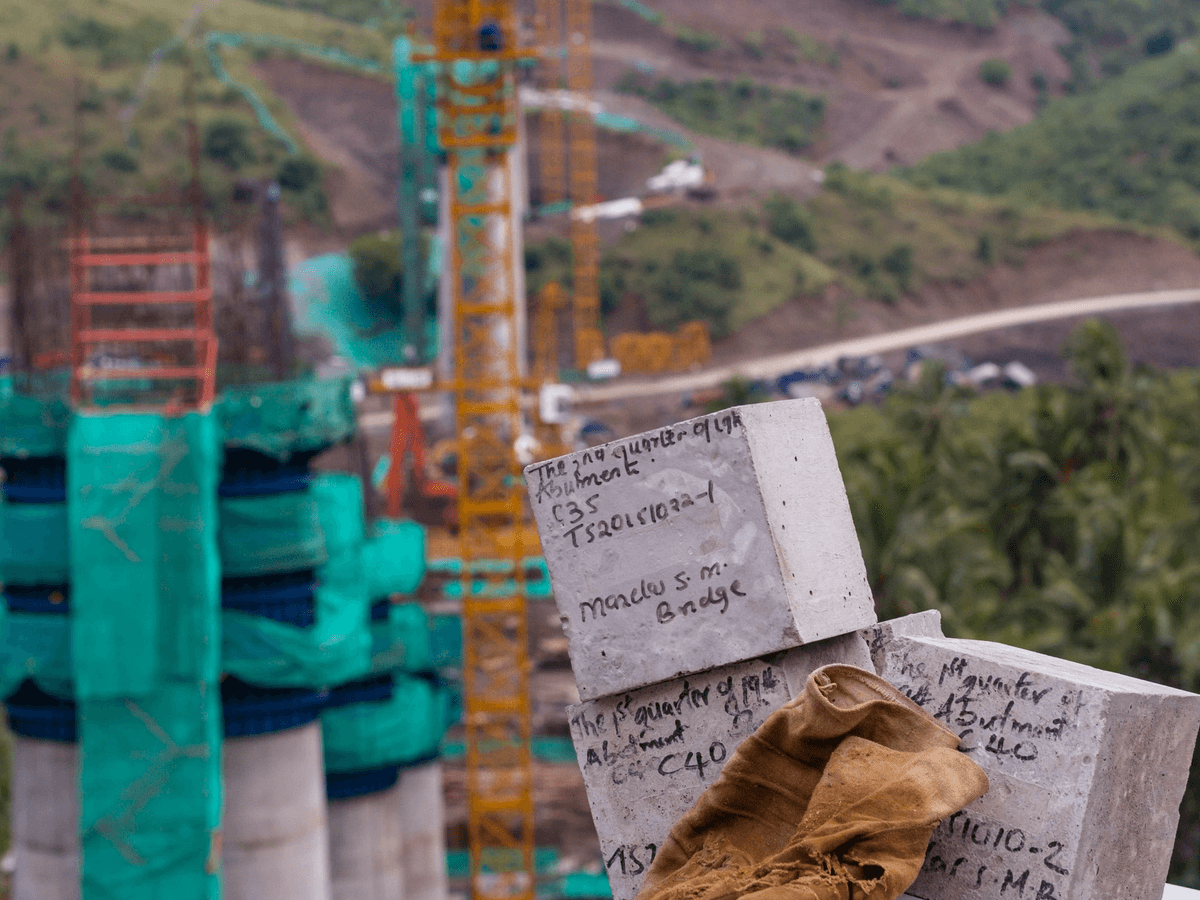
Quality control in construction is not just a box to tick; it's the backbone of any successful building project. Understanding the common quality control issues in construction is essential for ensuring that projects meet safety standards, client expectations, and regulatory requirements. By identifying these issues early, teams can implement effective solutions that save time and money while enhancing overall project quality.
Building or Structural Quality Issues
Building or structural quality issues are among the most critical concerns in construction. These problems can manifest as cracks in walls, uneven floors, or even compromised structural integrity that threatens the safety of occupants. Addressing these concerns promptly is essential because neglecting them can lead to costly repairs down the line and raise questions about why quality control is important in construction.
Quality Issues with Construction Materials
When it comes to construction, not all materials are created equal—some may fail to meet established standards, leading to significant quality issues with construction materials. Using subpar materials can compromise a project's durability and safety, making it crucial for teams to conduct thorough inspections and verify material quality before use. Understanding what constitutes acceptable material standards helps mitigate risks associated with poor-quality inputs and reinforces why is quality control important in construction.
Poor Workmanship in the Construction Industry
Poor workmanship in the construction industry can derail even the best-laid plans, resulting in defects that may not be immediately visible but could have long-term consequences. From improper installation techniques to lack of attention to detail, these issues often stem from inadequate training or oversight during various construction phases. Recognizing poor workmanship as a common issue highlights why quality control procedures are vital; they ensure that every worker adheres to high standards and practices throughout a project.
Benefits of Effective Quality Control
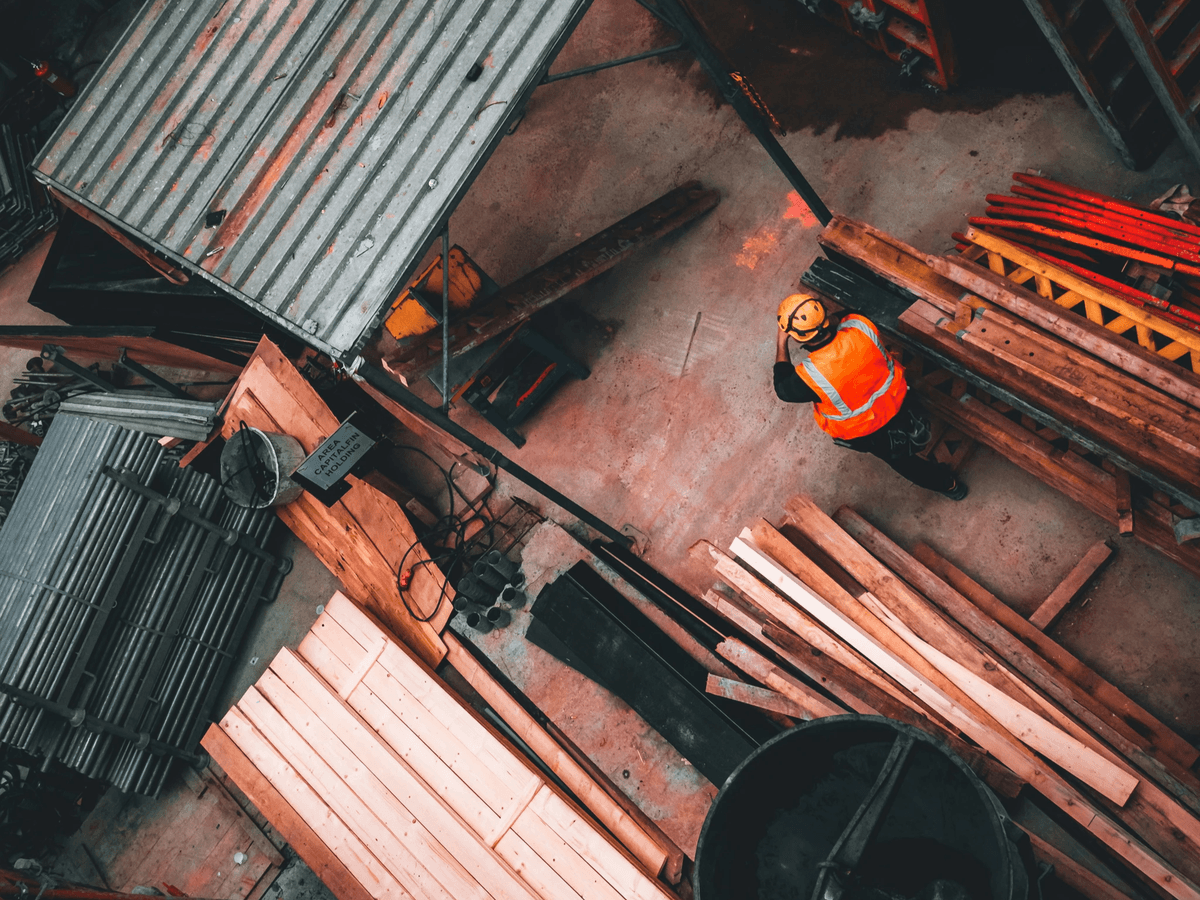
Effective quality control in construction is not just a box to check; it’s a pivotal element that can shape the success of any project. Why is quality control in construction important? It ensures that projects are completed on time, within budget, and to the satisfaction of all stakeholders involved. By implementing robust quality control measures, construction companies can avoid costly delays and rework, ultimately fostering a culture of excellence.
Cost Savings Over Time
One of the most significant benefits of effective quality control is the potential for substantial cost savings over time. When we explore what is quality control in construction, it becomes clear that investing in thorough inspections and testing upfront helps prevent expensive fixes down the line. For instance, addressing building or structural quality issues early on can save companies from facing hefty repair bills and legal liabilities later.
Moreover, adopting common construction quality control procedures streamlines processes and minimizes waste. By ensuring compliance with standards from the outset, companies can avoid disruptions caused by non-compliance penalties or having to redo work due to poor workmanship in the construction industry. Thus, while it may seem like an expense at first glance, effective quality control translates into long-term financial benefits.
Enhancing Safety and Compliance
Enhancing safety through effective quality control cannot be overstated; it’s crucial for protecting workers and ensuring compliance with regulations. Quality issues with construction materials can lead to hazardous situations if not properly addressed during initial phases. By rigorously testing materials before use and adhering to safety protocols, companies significantly reduce risks associated with accidents on-site.
Furthermore, why is quality control important in construction? Because it fosters a culture where safety is prioritized alongside efficiency and effectiveness. This commitment not only safeguards workers but also builds a reputation for reliability among clients and partners alike.
Boosting Client Satisfaction
Client satisfaction often hinges on how well expectations are met throughout the project lifecycle—this is where effective quality control shines bright! When clients ask what are common construction quality control procedures being implemented, they want assurance that their investment will yield high-quality results without unpleasant surprises along the way.
By addressing common quality control issues in construction proactively—such as poor workmanship or material defects—companies can deliver projects that exceed client expectations consistently. Happy clients lead to repeat business and referrals; thus, investing time into understanding why is quality control important in construction pays off handsomely as trust builds between contractors and their clientele.
The Role of Third-Party Inspections
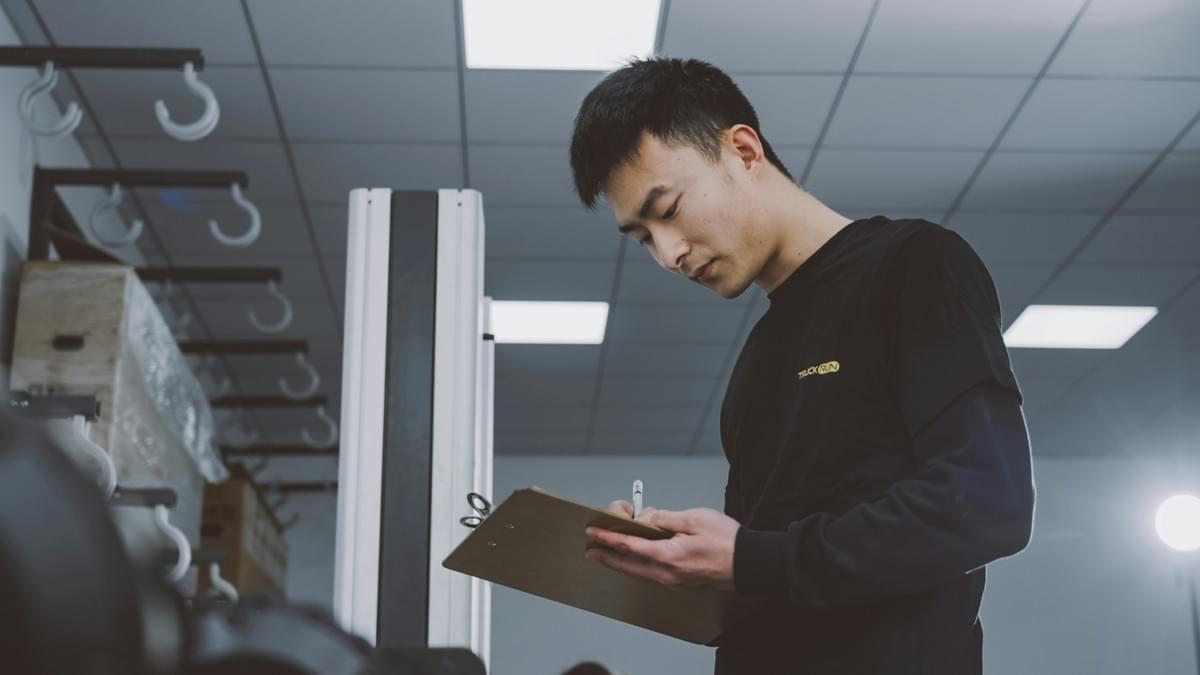
In the realm of construction, the role of third-party inspections cannot be overstated. They serve as an essential checkpoint, ensuring that projects adhere to quality standards and regulations. This is particularly vital when considering why is quality control in construction important?—it not only safeguards investments but also enhances the overall integrity of the built environment.
How China Inspection Pro Ensures Quality
China Inspection Pro stands out in its commitment to maintaining high-quality standards through meticulous inspections and assessments. By employing a team of experienced professionals, they conduct thorough evaluations at various project stages, ensuring compliance with established protocols and specifications. This comprehensive approach answers the question: what is quality control in construction? —it’s about verifying that every element meets or exceeds required benchmarks for safety and performance.
Advantages of Independent Verification
Independent verification offers numerous benefits that can significantly impact construction outcomes. For one, it provides an unbiased assessment that can identify common construction quality control procedures being overlooked by internal teams. Moreover, this impartiality helps mitigate potential risks associated with building or structural quality issues, ultimately leading to more reliable and durable structures.
Building Trust with Clients and Stakeholders
Trust is a cornerstone in any successful construction project, especially when addressing quality issues with construction materials or concerns about poor workmanship in the construction industry. Third-party inspections foster transparency between contractors and clients by providing documented evidence of compliance and quality adherence throughout the project lifecycle. As clients become increasingly aware of why is quality control important in construction?, they are more likely to engage with professionals who prioritize independent verification processes.
Conclusion
In the dynamic world of construction, understanding the significance of quality control is paramount. Why is quality control in construction important? It serves not only as a safeguard against potential pitfalls but also as a catalyst for project success. By implementing robust quality control measures, stakeholders can mitigate risks associated with building or structural quality issues, ensuring that projects meet both safety and compliance standards.
Key Takeaways on Quality Control
Quality control in construction is not just a checklist item; it’s an essential framework that governs every phase of a project. What is quality control in construction? It encompasses inspections, testing, and compliance with building codes to ensure that all aspects of the project are executed to the highest standards. Understanding common construction quality control procedures can significantly reduce the likelihood of encountering common quality control issues in construction, such as poor workmanship and material defects.
The Long-Term Value of Quality
The long-term value of investing in quality control cannot be overstated. Why is quality control important in construction? It leads to cost savings over time by preventing costly rework and enhancing client satisfaction through reliable outcomes. Furthermore, addressing quality issues with construction materials upfront fosters trust between contractors and clients, paving the way for future collaborations.
Next Steps for Effective Implementation
To effectively implement quality control measures, stakeholders should start by identifying what are common construction quality control procedures tailored to their specific projects. This involves training teams on recognizing common quality control issues in construction—like building or structural quality issues—and reinforcing protocols that prioritize excellence at every stage. Embracing third-party inspections can also enhance credibility; after all, who wouldn’t want an extra set of eyes ensuring everything meets those high-quality benchmarks?